CULVER’S STORY
Increased Task Completion Rates at Culver’s
Now taking temperatures is less than 5 minutes—start to finish.

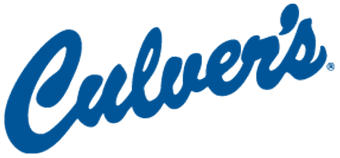
Original Problems
- Temperature checks not getting completed
- Lack of employee accountability w/ daily tasks
- Inconsistent customer satisfaction scores
The Results Using Jolt
%
Faster Temperature Checks
%
Increased Completion Rate
The Culver’s Story With Jolt
Culver’s Uses These Solutions
Jolt Lists
With Jolt Lists, your entire team naturally does the right thing, at the right time, in the right way. Turn guesswork into great work
Jolt Sensors
Discover a remote monitoring solution that protects inventory with alerts when temperatures fall outside of a defined range
Jolt Temperature Probes
Take and record food temperature in just seconds.
Jolt Information Library
Provide employee training and store content in one central hub.
Jolt Employee Scheduling
Scheduling your entire crew has never been easier than with Jolt’s drag and drop interface.
Jolt Labeling System
Streamline the label-making process by reducing the time it takes to make labels and eliminating errors.
See What Our Other Customers Have To Say:
Since implementing Jolt three years ago we have seen an increase in our inspection scores across all of our locations. Furthermore, Jolt has saved us thousands and thousands of dollars from failed audits, labor costs, failed freezer units going out, and so much more.
Our store recently got an evaluation from EcoSure and we received a Pride Award. The person doing the inspection said it was the cleanest Dairy Queen store they had ever seen.